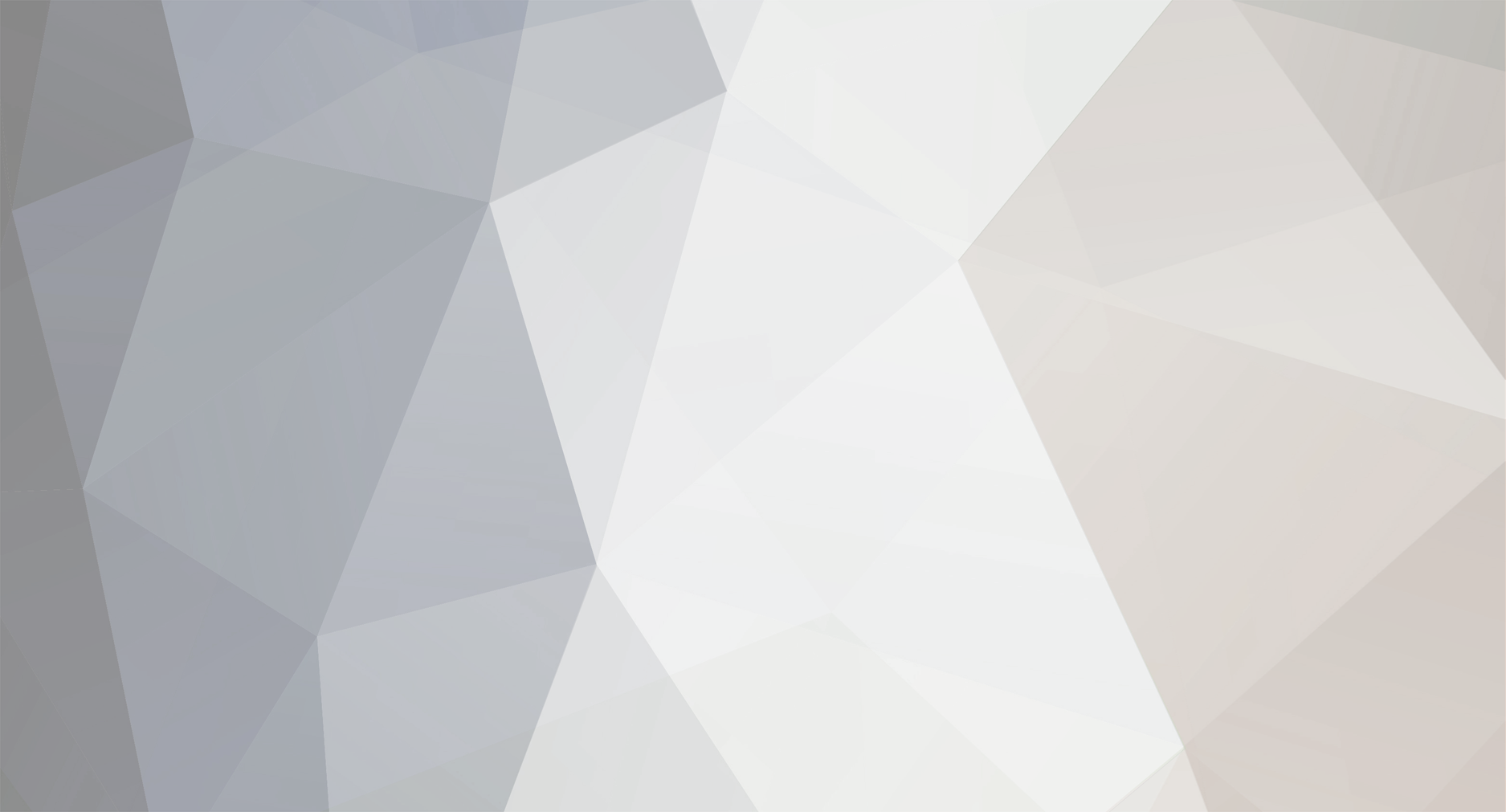
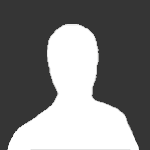
Rhyscar
Members-
Posts
923 -
Joined
-
Last visited
-
Days Won
1
Content Type
Forums
Downloads
Events
Gallery
Everything posted by Rhyscar
-
So these finally showed up. Pretty stoked to finally get them here. Big thanks to Phil/Fuel for shipping them direct to avoid paying a horrendous amount of GST through customs. GC So these are 3 way adjustable (hi speed & Low Speed bump + rebound) and is a similar design to the Reiger suspension they use in WRC/proper tarmac rally cars but at a fraction of the cost (Reiger's will set you back $5k per corner). I didn't opt for the external canisters as they were a considerable amount more, and won't be needed for getting used to the car and short hillclimbs I'll take part in to start with. I'd consider upgrading to the external canisters when I committed to something like Targa as the additional heat capacity of the oil will come into use when doing longer stages. After driving the daily on a local hillclimb I really was decided I had to do proper shocks if I wanted the car to have the potential to push my driving and take bouncing off the road out of the head-equation when attacking a dubious corner - more for when the unexpected pops up than when its planned but it will make or break how hard I can drive this thing. Should be indestructable too so looking forward to doing some big jumps with these Still need to buy springs from summit racing and get some tophats laser cut to suit so when my bank account recovers a bit I'll get them in the car.
- 418 replies
-
- 7
-
-
Check the backing plate behind the clutch. Could be touching the flywheel if not located on the studs properly. Also check if you've had the clutch out that the clutch plate isn't backwards. Both of these issues will have the symptoms you described.
-
Release bearing? Think you are looking too far into it. If it had run bearings you'd know about it.
-
Those paint protection films work awesome and you can also get a teflon coating on the paint to stop stuff sticking to it. Not sure if its gypsy magnet trickery or if it actually works though.. who knows. Parents live on a gravel road and have the paint protection film on a few areas of their WRX and it seems to have lasted pretty well.
-
Same here... rev limit 37 times in 2min period... whoops must have slipped on loud pedal... in 3rd gear. Dammit.
-
+1 for start with the wheel speed sensors. See if you can get a scan tool on it to read any faults it's logged regarding the abs. Shuddery brakes will come back eventually. Proper fix is to back the adjustment off the master cylinder at the back of the pedal box. 2-3mm is all it needs so it doesn't give too much play in the pedal. For some reason they all came quite poorly adjusted from the factory.
-
Oh man that sucks!
-
If your still having issues with shifting the only other thing worth checking out is the clutch plate and make sure it's not cracked. Replacement plates are real cheap from Toyota and don't normally crack cause they are made by exedy but I have had it happen before with a shitty pbr clutch plate where it wasn't shifting right for a while before it finally decided to explode at manfield. Sorry for the wall of text. Hopefully some of it is helpful.
-
Oh easy was to get that shaft out is to undo balljoints bolts and swing strut out, splitting the inner cv on that drivers side. Half shaft will then come out easy as. Just need to repack cv with grease and make sure you get the band done up nice and tight which is easy with those Toyota clips on there or a good thick cable tie works fine for a certain amount of time also.
-
Rebuilding the gearbox is relatively easy especially if your only doing bearings. Pull the end cap off, take to gearbox shop and get them to pull reverse and 5th gear off the end of the shaft as they require very particular gear pullers to get them off without damaging them. Normally costs a few beers. Pull shifter linkages and mechanism out next (4x bolts where shifter shaft goes in). Pretty sure from here the casing can be split once you undo the one bolt on the front of the gearbox housing - someone correct me if I'm wrong but there's something funny about that one bolt iirc. Pretty easy to pull shafts out and press/pull bearings out of the housings. Can buy a lsd brand new from Toyota around $450 for a standard one or $1250 for a TRD plate type diff. (mark can confirm pricing) Bearings seem to be about $100/ea but Def worth replacing including diff bearings. Just remember to use feeler gauges to measure tolerances between gears/synchros before pulling apart so you don't put the gears back on too tight. You'll need to replace to circlip under 5th gear also when it goes back together these are a one use only circlip. Memory is a bit hazy been 5 years since I rebuilt my old c56. Found a manual online and gave it a go with no precious experience wasn't too hard at all. I highly recommend a TRD diff you won't regret it helps the handling of the car so much. Also Kaaz and cusco do similarly priced diffs too, Kaaz being slightly better quality imo but slightly more expensive too
-
Here is a seal showing the inner face it seals on (they cross hatched type looking one) - pic looks slightly exaggerated might be from an MR2 box but it looks pretty much the same And see the shoulder on the shaft here that it seals on (at bottom left of pic - sorry couldn't find a bigger one) To be sure of installed location of that shoulder you could take shaft out, measure to inner seal from hanger bearing mating face then measure corresponding shoulder length on shaft from same hanger bearing mating face. Another thing thats caught me out before is having an extra dowel on a box/block where it didn't have a hole for one. Meant the last 5mm never pulled up as it bottomed out on the dowel. That ended badly with suspected run bearings but I always check any new bellhousing now! something worth checking out anyway. There are two different hanger bearing brackets - one for auto and one for manual, although the auto ones are 4-6mm out of alignment and make it pretty near impossible to install the driveshaft unless you are being super rough with it. The one that was in the car was definitely a manual one so I wouldn't worry about it.
-
I had that same thing happen when I put that box in.Turned out to be an hard old seal that was cracked. Replaced the gearbox seal and it stopped leaking. The seal doesn't do its 'sealing' against the dust cover, there is about 10mm of flat shaft on the driveshaft before it drops down to the spline which it seals on so its location can be +/-2mm and it would still seal fine. If you are careful with getting the seal out of the one which was in the car you should be able to reuse it. If not get hold of corollaGT he will get you one fairly reasonably priced! Sucks about the synchros. Never had any issues with shifting and with my other cars these synchros seem to take quite a beating before they give up. Getting the master bled correctly can sometimes be tricky/time consuming if it has gulped some air.
-
I did the exact same trip in my coon a year ago but in reverse. I've got pics in the exact same places as yours almost exactly to where you parked... haha bringing back good memories. Glad to see you enjoying the car it makes me much happy. Make sure you do the road from Wanaka over to Haast its amazeballs. Best road I found while I was down there - slightly better than hooning around Caitlyns. Did it in about 1hr 15mins I was trying quite hard and managed to wear through 5mm of tyre tread in the 300 odd kms had to get a new set when I got to Invercargill.
-
Favour needed - pick up a car and store for a week?
Rhyscar replied to Rhyscar's topic in Lower North Island Region
Car is located in lower hutt. Fully understand if too much of a pain in the arse. Pretty sure sunday will be fine - just checking- 6 replies
-
- beersies
- help needed
-
(and 1 more)
Tagged with:
-
Favour needed - pick up a car and store for a week?
Rhyscar replied to Rhyscar's topic in Lower North Island Region
Thanks heaps man. Will talk to the guy and see if tomorrow suits him and find out what part of town he is in. I'll fly down first thing on the sat morn so should be pretty hassle free.- 6 replies
-
- beersies
- help needed
-
(and 1 more)
Tagged with:
-
Hey Oser's Just doing some fishing if someone can help me out. Have bought a lush daily to kick around in but it is looking unlikely I will be able to get down there this weekend to pick it up but can make it next weekend. http://www.trademe.co.nz/Browse/Listing.aspx?id=1129017317&open_homes=®ion=&district= So if someone has the means of picking up a car and storing it for a week it would be awesome. Will return the favour in beer and/or parts transport from anywhere up here down the country when I fly down if that would help anyone out? If anyone is keen I'd be super grateful. Cheers, Rhys
- 6 replies
-
- beersies
- help needed
-
(and 1 more)
Tagged with:
-
some silicone sealant will work fine? Get the 300deg rated stuff and it'll never leak..
-
Good to know. Wonder if there are any units that have already been approved? Quite a few rally cars have them but most aren't certed with them in..
-
Design approval for the manufacture of the internal gearing/shafts or for the mounting of it? I was under the impression they were a big no-no
-
Thanks heaps man! legend
-
Not entirely convinced. Thoughts?
- 418 replies
-
- 2
-
-
Whats happening here?
-
125 deg is OK for your oil as long as your aware it will break down quicker the more time it spends over 100deg. We've seen up to 170deg after 2 laps with a looped oil cooler lines (due to hole in cooler). Brand new motul V300 was toast after 2 laps at this temp and had to throw it away for next race (smells burnt as shit and weird consistency) Big difference between the brands of coolers. Mocal are OK but over 15-20deg less when using a setrab/greddy seem to be the best. Try over filling the diff by as much as you can to help keep everything lubed up during cornering. We use the redline shockproof in my daily coon and the rally car. Both take a beating and seem to handle it OK. Not convinced on the redline though have seen some pretty nasty wear in different applications. Don't know if that could be put down to the oil though.. Motul is the closest spec to TRD you will find. Worth its weight in gold (toyota might do it relatively cheap - I know they do motul brake fluid cheap as!). Weir performance make new CW+P's in the states. Bout $300usd isn't so bad. I'm ordering a 5.1 for the rally car soon... Don't buy shit oil kids. Also love this car. Please enjoy more.
-
Beginnings of shaping some things. Airbox Sandwich
- 418 replies
-
- 1
-
-
Clearance isn't as bad as I was worrying about Starting to shape an airbox that will fit in the cutout below and the inlet for it will be on the passenger side. I'll still consider using a curved trumpet depends on how the airbox comes out. I'm still aware a curved trumpet may help airflow within the airbox considerably but will see if I can make these trumpets work first. I'll use a half sized civic radiator in the middle somewhere and oil cooler on the left. I'm keen to vent each one through the bonnet to make sure engine bay temps don't get too high. May need to make sure I create enough of a low pressure area for bonnet vent that cooling isn't hindered at high speed.. hmm Time to start a carbon fibre manufacturing facility in my shed I think. Should be interesting
- 418 replies
-
- 3
-