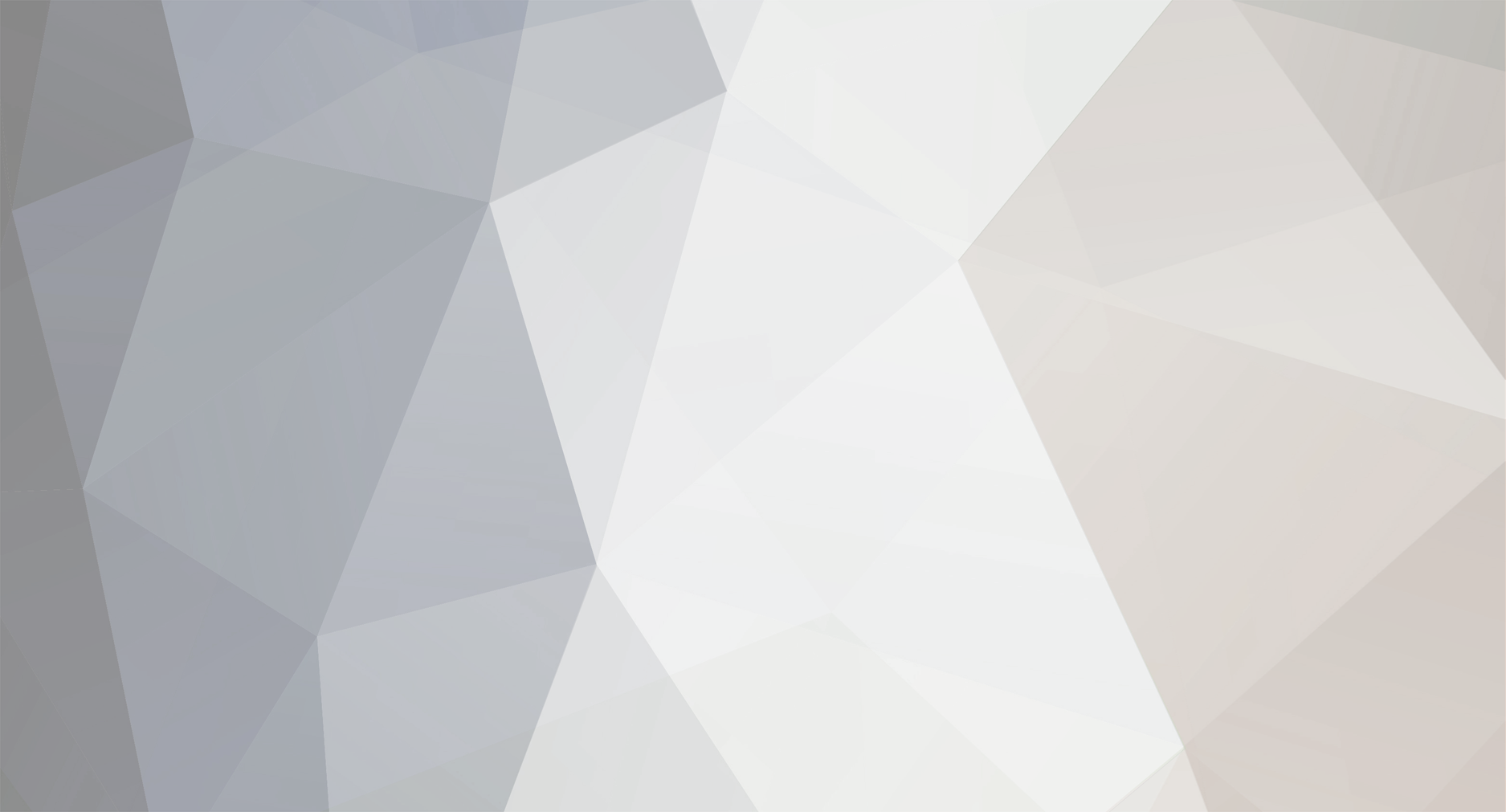
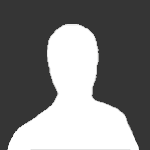
nothingsfree
Members-
Posts
510 -
Joined
-
Last visited
Everything posted by nothingsfree
-
nothingsfree's Toyota Corolla Ke70
nothingsfree replied to nothingsfree's topic in Projects and Build Ups
Craig dropped round a pair of my revised rear caliper brackets. So I bolted them up to the pair of skyline 2pots that I picked up off trade me that have been half painted. Due to the size of the caliper, and how much the outer piston sticks out, I have to run a 25mm spacer to get my Longchamps to fit. Even then, I had to grind the Nissan off the outer face to make sure there was enough clearance. But running a spacer means the wheels now tuck very nicely just inside the flares. So with my 13inch rim on, everything clears with about 4mm to spare. -
nothingsfree's Toyota Corolla Ke70
nothingsfree replied to nothingsfree's topic in Projects and Build Ups
I finally cut my rear guards out fully to where I needed them. At this height, the arch actually goes through the rear door now by roughly 20mm. This gives me 55mm clearance before the tire hits the arch. Obviously the tire will hit the flare before it gets that far, but it allows decent clearance, and Im ok with damaging/blowing off flares. Its means I can still run the guards/tires pretty close without serious repercussions. Started cutting up my rear doors as well. It seems so wrong cutting up straight/rust free Corolla doors, but they are all I have, so under the grinder they go.. I am going to be running Lexan in the rear doors and rear window, so there is no need for winder mechanisms or any of that rubbish, so I pulled it all out, and then cut out the inner skin. I will also have to cut 20mm off the arch and weld it up as that is how much higher the flare is sitting. -
Cheers bro. Sorry unsure of what model the diff was out off as i bought it as a bare diff. The engine hasnt been tuned yet, but it will be going to NZEFI when it is ready. Currently it is running on the map that Surfab had on his Link for his 3s. But you can load on a base map that will be enough to get the engine running at least if you buy a Link. Yeah cage is near the top of the to do list now, hopefully in Dec sometime.. No other vids at the mo, but hoping to have an exciting update in the next week or two..
-
Hey Nick, drop round sometime for a yarn, got a few things you maybe interested in..
-
^This. Im running Wilwood Dynalites with a 255mm x 20mm rotor under my 13inch Longchamps. You wont get much bigger than that under a 13, iv only got bout 4mm clearance around the circumference. Otherwise my old setup was pretty decent, Nissan Laurel large single pots with a 256 mm rotor..
-
nothingsfree's Toyota Corolla Ke70
nothingsfree replied to nothingsfree's topic in Projects and Build Ups
So this happened a few weeks ago... First time in four years this car has made any noise! Still a long way to go, but it feels like a massive step forward. -
Yeahhhh buddy, go Team 70!
-
nothingsfree's Toyota Corolla Ke70
nothingsfree replied to nothingsfree's topic in Projects and Build Ups
Decided to run bigger calipers on the front as well.I couldnt go any larger with the diameter of the rotor because of the 13s. So I am sticking with a 256mm rotor. The issue I have with running a larger caliper, is fitting them behind the Longchamps. Because they have such a flat face where they bolt to the hub, there is very little room. But by modifying the rotors so they can bolt to the inside of the hub, like they do on a factory ae86 hub, it gives enough room to fit a Wilwood Dynalite 4 pot caliper, just. The rotors I was running on the front dont have the right offset, so I am using those on the rear, and after some measurements found some other 256mm rotors that were suitable. Once again, it was off to Royce Clive, to have the center hole bored out to fit the back of the hub, and holes drilled so the rotor could be bolted to the hub. Kev had the rotors back to me the same day, so thanks again to Royce Clive Engineering for all their help and fast work! With the rotors bolted to the back of the hubs, and the hubs back on, I could test fit the latest purchase.. I slid the caliper onto the rotor and tried on one of my 13 inch Longchamps, to make sure everything was going to clear, and it does, with about 3mm. Then I could start taking measurements to figure out making the caliper mounts. -
nothingsfree's Toyota Corolla Ke70
nothingsfree replied to nothingsfree's topic in Projects and Build Ups
Started the brake upgrade. At the back Im using Nissan 2pot rear calipers with 256mm vented rotors. So I dropped my axles off at Royce Clive Engineering to have the hubs machined down to allow the rotors to slip over. While Kev was at it, I also got him to check the alignment of my diff housing, and straighten it, as it is common for them to warp after welding. With that all done, I bolted everything back up and started taking measurements to make my caliper mounts. I used a caliper mount that Surfab uses for mounting Bluebird calipers to hilux diffs. It wont bolt on, but it gives me a starting point, and something that will bolt to the diff. After cutting the ends down to suit the smaller rotor, and some more measurements, I drilled some more holes for the caliper. This meant I could sit the caliper in position on the rotor, and gives me a chance to figure out how far I need to offset the mount so the caliper is central on the rotor. -
Also, Iv decided to upgrade my front brake set up (again), so if anyone is interested in a decent upgrade for ae86 struts, let me know..
-
Cheers boys, yeah getting there slowly. This thing is an exersise in doing things the hard way because of the wheels I wanted to run, and the height I wanted it at, while still making it work properly haha.
-
nothingsfree's Toyota Corolla Ke70
nothingsfree replied to nothingsfree's topic in Projects and Build Ups
More work on the fuel system. I needed to finish off my fuel tank so I could get it back in place, to measure up and cut my fuel lines to suit. To get it ready to fire up, I needed to install the fuel pump and sender so I could seal the tank, ready for fuel. I had an Autometer sender and gauge, but it had no seal, so I had to buy a roll of cork, I coudnt just get a little square haha. Then it was on to the other components of the fuel system that I have been collecting.. The fuel line comes from the tank, through the firewall, into the fuel filter, which is the large silver cylinder under the intake flange. It is a copy, that takes direct replacement Aeromotive filter elements, which are great for not killing flow. Then it takes a 90 degree turn, and then another, into one end of the fuel rail. At the other end of the fuel rail, it takes another 90, into the Tomei fuel pressure reg, before heading back through the firewall back to the tank. I had a small length of black braided line, and a black straight fitting left, so I got Surfab to weld on a -6 to the top edge to use as a breather. For testing, I left the tank out beside the car, so I could check for leaks and any other issues. -
nothingsfree's Toyota Corolla Ke70
nothingsfree replied to nothingsfree's topic in Projects and Build Ups
I started work on my intake manifold, but before I could commit and get something cnc'd, I needed to sort out the throttle bodies. I definitely wanted to run black top throttles, as the extra 2mm diameter certainly adds up across the surface area, especially with four of them.The downside is the funny shape at the exit of the blacktop throttle bodies. Which leaves you with three options. Blend the shape of the t/b into the manifold flange, change the shape of the t/b, or leave it. Particularly with a N/A engine, you want the air flow disturbed as little as possible, so option three was a no go. I decided to change the shape of the throttle body. I carefully cut into the t/b where the shape changed from round to the odd shape at the exit. I didnt cut far into it, just enough to allow the metal putty to not be too thin. I also drilled four holes around the diameter to give the putty something to lock into. And finished it by sand blasting to give the best possible surface to bond to. I mixed up the putty, and worked it into the end of the t/b, making sure there was plenty of excess, and left it to set under gentle heat. After curing for a couple of days, I took the throttles to Craig Young at Young CNC Machining Ltd. Craig clocked up on the internal 45mm diameter and then machined out the putty. So now there is a nice smooth 45mm diameter along the entire length of the throttle bodies. Which makes it much easier to make a manifold for, and will disturb the airflow less. This is the start of the intake manifold, Craig designed and machined up the flange that the throttle bodies will bolt to. The flange will then be welded to runners, which will be welded to a modified version of the factory flange that bolts to the Beams head. Thanks again to Craig for his work, an excellent job, at a very reasonable price, and real keen to help. Will be seeing some more work from him soon.. -
nothingsfree's Toyota Corolla Ke70
nothingsfree replied to nothingsfree's topic in Projects and Build Ups
Had to do some further modifying to my cooling system. My radiator fits really nicely in the factory hole in the radiator support panel, but with the height of the 3sg, the filler neck on the rad is far from the highest point. I wasnt keen to lift the rad, as it fits sweet where it is. But I also didnt want issues with filling/bleeding the cooling system. So the best option was to cut the rad cap/filler off the rad and move it to the highest point, the top water pipe on the engine. After cutting off the filler, and making a new neck for it to sit on the pipe, I got Surfab to weld it on, and a new blank plate for the top of the rad. -
nothingsfree's Toyota Corolla Ke70
nothingsfree replied to nothingsfree's topic in Projects and Build Ups
And so begins the next saga in the build. Wiring the car up from scratch. I did a big buy up of all the bits I would need, relays, bulbs, wire etc... And of course, the Link engine loom. Then Max and I got to it. I want to keep it simple and easy to diagnose, so all the relays will be mounted on a bracket, and are all fused and easy to get to. The switches are also pretty simple, being a race car, it had to have a push button start haha. Im only putting back in, what is necessary to run the car, and to be road legal, horn, lights etc. Running from the back of the car, there is only tail lights, brake lights, indicators, number plate light, fuel sender, and fuel pump. From the front there is lights/high beams, indicators, rad fan, horn, and wipers. And then the engine loom separate. -
nothingsfree's Toyota Corolla Ke70
nothingsfree replied to nothingsfree's topic in Projects and Build Ups
So I ran into another issue relating to ride height haha. At the height I want it, my HSD rear suspension wont fit, it doesnt go low enough. Even with the adjustable spring hats removed, and the springs compressed and sitting straight on the diff, its not quite enough lol. I could make up some towers that raise the springs into the body, but its not really worth the effort. So anyway, a friend of mine was wanting to put adjustables into her dx, so she bought a set of XYZ coilovers, and I swapped her the rear coil overs for my separate coil and shock set up. With the shock mount moved further down the lower arm mount on the diff, it give plenty of room for adjustability, both up and down from this height. And as the cage will be tied into the rear shock tower, there isnt any issues with strength of the floor. -
nothingsfree's Toyota Corolla Ke70
nothingsfree replied to nothingsfree's topic in Projects and Build Ups
With the car at this height, there is no way the factory panard mount will work. At static height, it is already well past horizontal. And having seen the factory ones start to pull away from their spot welds, it was probably worth modifying anyway. So I drilled out the spot welds on the standard one, and removed the entire mount from the body. With the diff sitting at the correct ride height, I sat the panard bar just under level, and took some measurements for making up a new mount. I then cut two of them out of 5mm steel, and another piece as a brace between them. After drilling a hole through both pieces, I welded them the chassis, and then welded in the brace. After setting it up, I decided to drill a second set of holes through, to give more options at different heights. -
nothingsfree's Toyota Corolla Ke70
nothingsfree replied to nothingsfree's topic in Projects and Build Ups
I dummied up the fuel tank in the boot, to get an idea where it would sit in relation to the exhaust. I added a length of box section between the chassis rails at the back of the boot floor. This would be used to mount the straps to hold the tank, but I also added a length of rollcage tube straight down off the box section to work as a rear jacking point, as there is no way of getting the jack under the diff with the height its at. I got a mate to cut and fold up a new flat boot floor for me. It has a ridge running forward on the angle which gives the floor some more strength, and allows enough room for the wiring and fuel lines to run along the top of the tank, out of the way. With that all sorted I bent up some stainless straps to hold the tank, and mounted everything. -
nothingsfree's Toyota Corolla Ke70
nothingsfree replied to nothingsfree's topic in Projects and Build Ups
With the diff in place and the car at the height that I wanted it, I now had to try fit an exhaust under there. The Tanabe headers merge into a 2.5 inch tube, so I picked up a length of 2.5 inch stainless tube, a flexi, a v band, and a couple of stainless crossflow mufflers. I tig'd the vband flange to the end of the headers, and the other side of the flange to the flexi. I then spent ages messing around trying to fit the exhaust up into the body enough that it wouldnt be the lowest point. With the help of a BFH I managed to encourage the floor up in several sections allowing the mid muffler to sit higher than the chassis rails. With that tucked in, I could mock up the rest of the exhaust, making sure there was clearance from the floor, diff etc, but still tucked up enough to not scrape. With everything sorted, I tacked it in place, before pulling it out to weld it up completely. Iv done a little tig welding, but this was my first exhaust, certainly a little more difficult than welding flat plates. Was good fun tho, and hopefully it holds together haha. Iv left the last section that will stick out the back of the car until I can take it for a drive and make sure that the exhaust is going to be fine where it is and doesnt need further modifying. I built the exhaust when I still had the intention of it being a road car, in hindsight there is a couple of things I would do differently, rather than bash the floor up to make enough clearance, I would just make a tunnel down the passenger side, and I would prolly run only one muffler. But I'l get it going, and then look at changing it.. -
This is probably the route Im going to take. The decrease in oil is pretty minimal anyway. Nick, yeah it is something I was wondering about, but I havnt really looked into it. What sort of coin are you looking at for a suitable setup?
-
nothingsfree's Toyota Corolla Ke70
nothingsfree replied to nothingsfree's topic in Projects and Build Ups
The Beams 3s is a really tall engine, it fits quite well into the ke70 engine bay, but there certainly isnt alot of room to move it any further. I have set my a little lower and further back than usual, but this meant that the sump is sitting down below the cross member. Obviously with the car sitting so low, that was never going to end well. So time for some more cutting.. I went around the sump with masking tape, so I could stretch it out and get a straight line that was easy to follow with the grinder. And then measured up 5mm along the front, and 20mm at the back and ran another length of tape around. this would pull the sump up flat, and get it slightly higher than the crossmember. After tacking it in place and making sure all the edges lined up, it was time to weld it fully. The oil pick up only need a slight bend to suit the new sump. -
nothingsfree's Toyota Corolla Ke70
nothingsfree replied to nothingsfree's topic in Projects and Build Ups
After getting my diff back in, I could drop the back of my car to the sort of height that I want to run. Which immediately ran into issues, the tires were sitting hard on the rear guards, so it was out with the grinder again. I cut off along the edge of the door line and then continued around, which is about 10-15 mm above the upper radius of the arch. I lowered the car back down, but it still wouldnt roll. It turns out at this height, the drive shaft is sitting on the tunnel. So I took to the tunnel with the grinder as well. Surfab folded up a new rear tunnel section to suit, taller than factory, and to match the tunnel section he had folded up to fit over the gbox. Same as the front section, I pushed it up through the hole from underneath, tacked it in place, and then worked my way along pushing the new tunnel out against the side of the old tunnel, and welding it in place. Then trimmed the excess from the underside. Now I have room for the wheels/diff/driveshaft to travel, without hitting anything. Although I will have to cut more out of the rear guards to allow more room for travel, currently there is only about 15-20mm between the tire and the arch I have cut. This will mean that I am going to have to cut into the door, and raise the arch further in the body/door. But I'l deal with that later, its rolling at the height that I want at least.. -
nothingsfree's Toyota Corolla Ke70
nothingsfree replied to nothingsfree's topic in Projects and Build Ups
Had some 2jz engine mounts lying round, so decided to modify them to suit my set up as they are alot firmer than the factory 3sg ones. 3sg on left with one bolt cut off the bottom, and 2jz on the right. The top bolt that goes through the engine mount is just the same, so no issues there. The bottom one is significantly larger on the 2jz. So I just had to re drill the hole through the mount larger, and drill out the hole underneath through the cross member for the nut to thread on. -
nothingsfree's Toyota Corolla Ke70
nothingsfree replied to nothingsfree's topic in Projects and Build Ups
The next step for the tank, was making up a swirl pot to sit in the bottom. Like I said, I want to keep it simple, so I didnt want to run an external surge tank that would require more fuel lines etc. So Im effectively mounting the surge tank inside the fuel tank. Hopefully it will work, will find out once its driving I guess. So Surfab rolled up a piece of alloy to suit. I pushed it up from underneath with the fuel pump sitting in place until the bottom edge of the tube was nearly flush with the pick up. The round piece I cut out of the bottom of the tank, will now be welded onto the bottom of the tube. The height of the tube means when the tank is above half full, it will always be submerged. Below that point, the swirl pot will rely on the fuel return which also feeds into the pot, and 6 holes drilled around the tube that sit flush on the bottom of the tank. It is simple, now to see if it works.. -
nothingsfree's Toyota Corolla Ke70
nothingsfree replied to nothingsfree's topic in Projects and Build Ups
The factory fuel tank wasnt really going to work with my setup. With the boot floor cut out, and the need for an upgraded fuel system, it was better to just make something new from scratch to suit. I want to try and keep it as simple as possible, and so I am running a rx7 intank cradle and pump. This will sit in a tube inside the tank. Im hoping this setup with be sufficient, and not have any issues with surging, but if it does, then at least it will be easy to just add an external pump and small surge tank. The pick up will sit below the bottom of the tank, and the tube will poke through to act as a bowl. Where the tube is level with the bottom of the tank, there will be a number of holes in the tube, to allow fuel to drain into it, as well the being fed by the fuel return.