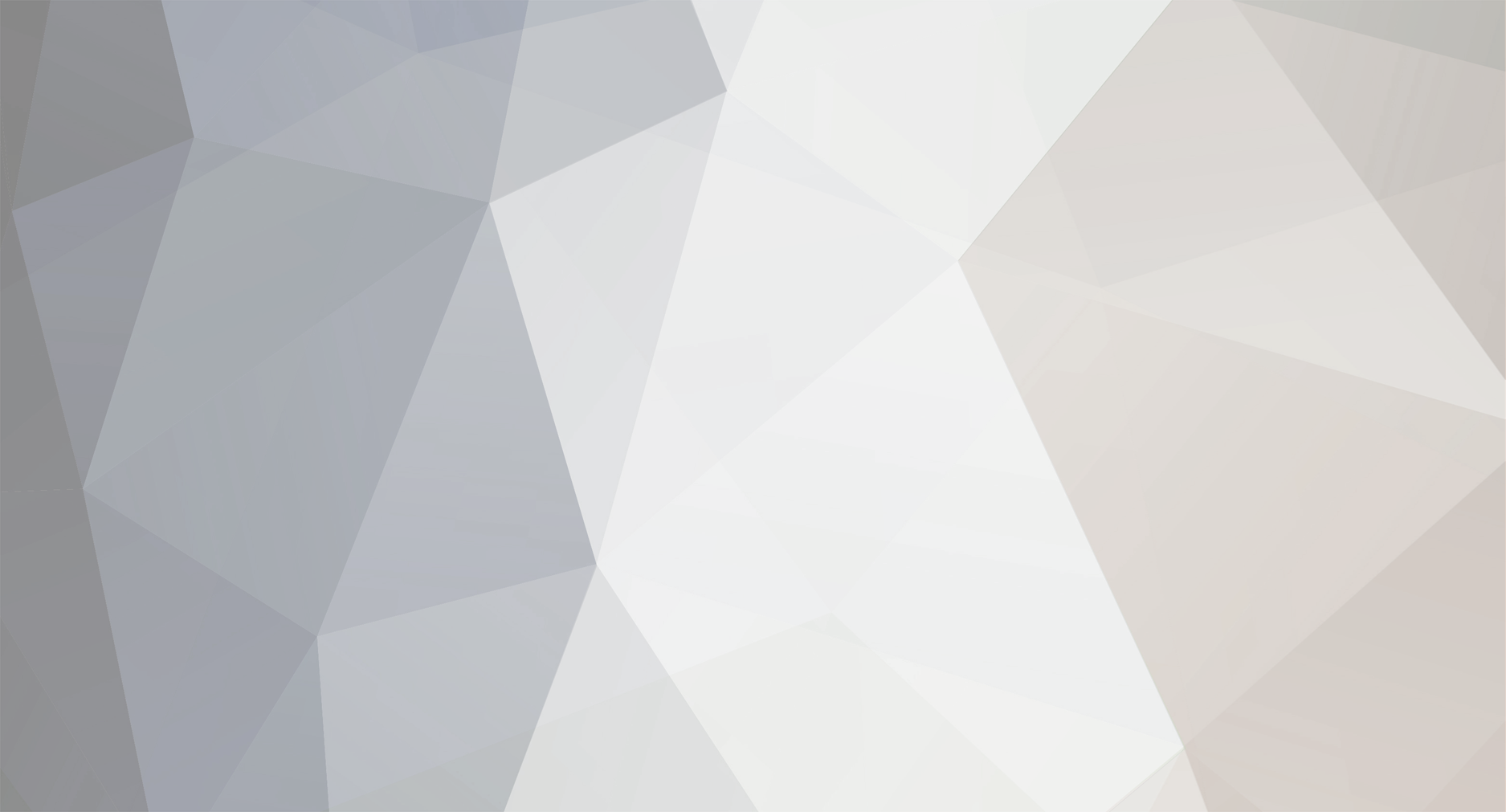
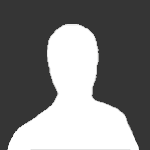
Hyperblade
-
Posts
345 -
Joined
-
Last visited
Posts posted by Hyperblade
-
-
2 hours ago, h4nd said:
PM me, I may have time Wedns, or maybe loan you a scope and show you the "Auto" button.
Hall effect? Can you jig a wheel/cog into a drill /vice?
Yep Hall effect, it's positioned directly against one of the gears (nothing special I can see on the gear)
I don't know the size of the gear it's against, so not sure how accurate it would be replicating it, I could 3d print something, but I assume you have to put some metal in it for it to work.
I think it needs to be fairly high rpm to recreate the issue, I think outside the range of most drills/lathes.
Have PM'ed you
43 minutes ago, NickJ said:I also have a small scope that would happily see that, won't be until next weekend that I would be free though.
Thanks I'm in no rush so If h4nd and I can't work something out will give you a bell.
-
I need someone with an Oscilloscope and who knows how to use it to come round and help me diagnosis a speed sensor cutting out at 5000hz (120km/hr+) (according to the Link ECU).
It's in a racecar so I can't drive it on the road, however I can recreate the issue on the jack stands, and I have a DTM connector (and know the pinout) in the engine bay to the sensor so will be relatively easy to intercept the signal?
It's a Honda s2000 AP1 gearbox, and a Link G4X Xtreme X which has been double checked by link (capable of 10,000hz)
I also have a spare speed sensor that can be bench tested if required.
I can only do this during the day either during the week (I work from home most days) or weekends as the car is to noisy for the kids/neighbors...
I'm located in Prebbleton and happy to pay for your time.
-
So since it's of the same era. I've wired up a 84 Toyota starlet motor from scratch before, which was a pain.
Here's a starlet wiring diagram.
\
In my case I needed a 4 pole switch (not cheap e.g. $80+) to allow it to park correctly, getting off/low/high is the easy part.
The wiper motor needed 12v and 3 wires from switch.
Pin Terminal Cable Destination Description 1 12v 12v Light Blue 2 park Light Blue/White 3 low Light Blue/Red 4 high Light Blue/Black Then the switch needed 12v as well then 3 wires to the wiper motor and you have to jump 2 of the pins (dotted)
Pin 2: Park
Pin 3/4 connected via jumper (dotted)
Pin 5: Low
Pin 10: (not sure can't read what I wrote, I think it livens up the other circuits within the switch
Pin 11: 12v source
Pin 12: High
-
1
-
2
-
-
8 minutes ago, shrike said:
Keen for start up/running videos and shed skids
Are your J160 all stock internals? Or have you had some mods done (Circlip?) Any idea how it'll go with many revs?
I'm assuming power and torque are within specs for it?
A friend races his RX7 with a 13B and a J160 and it's been pretty reliable for the most part (he's raced it since 2008).
However last round he blew 4th gear, so the circlip mod may be worth looking into.
The issue is a lot of the boxes for sale are all very high k's and it's not as easy as it used to be to find cheap good condition ones.
-
RE flywheel, I'm not up to speed on it all your issues, but could you run an insert like the K2F flywheels run (inserts can be bought separately)?
-
2
-
-
4 hours ago, Honda Ass Dragger said:
TBH the G5X is a bit of a disappointment
It still requires driver boxes for DI - where as a Motec doesn'tYeah and for the price you don't even get a PDM built in. On the flip side at least g4x maps transfer over and plug a and b are same as g4x series so easy upgrade. But a bit underwhelming tbh.
-
1
-
-
11 minutes ago, shrike said:
Also I'm not sure of an aftermarket ecu that runs direct injection but I could be wrong
Link have had one for a while
G4+ Force GDI https://dealers.linkecu.com/force-gdi 4 Cylinder only though, ($3000+)
And have their new G5 Voodoo Pro https://dealers.linkecu.com/G5-Voodoo-Pro ($5000+)
Not a cheap exercise!
-
12 hours ago, Roman said:
Yeah I'm using SW20 calipers at the moment with a Primera disc.
But I've got an MX5 setup here I was looking to fit at some point.
Going back to a smaller/lighter non vented disc, and better pad options for MX5s.
That's one of the most important things for choosing a caliper I think, finding something that actually has good pads.If using anywhere near the track then yep it's a big deal, if you make sure you have a good range available you will save yourself a lot of money in the long run.
More choice means more competition so harder for the manufacturers to price gouge you.
So calipers from MX5, GT86 etc are good choices as they are often tracked as standard.
1 hour ago, mjrstar said:There are places like carbotech that will reline backing plates to whatever you supply (if they don't have an off the shelf for you). I run thier xp8 series in my civic which are legit in my opinion..
Generally though you are still limited to a smaller selection of compounds, my personal experience of bonded mintex was not a good one. But it's going to also depend on the use case, as proper track racing is quite different to say hill climb or street.
Another option is picking a caliper that lets you water jet cut a pad down from another common pad size, this is what I did with my rear AE86 disk setup, I just had wilwood polymatrix pads cut down to suit, $25 to cut down per pad, and once they have template it's easy as.
If your looking for long lasting brakes, bigger and thicker pads are what you want to go for, it helps them last a lot longer from the heat and just helps all the components around them.
-
2
-
-
17 hours ago, Tiger Tamer said:
It would have to be all set at the same height as it is now as the boot floor is directly above the tank. It could be done as he has done it or finding something from another donar car. I have sealed the inside of the tank with POR15 so it would have to be stripped out to be able to weld to it somehow as being able to reach it would be a problem. I would think there maybe some cert requirement coming to welding fuel tanks mods, but don't know for certain.
This is what he did with the S2000 pump. First pic is with the piece he cut out to shorten it.
That looks like a nice simple self contained approach definitely worth exploring further, when you add up all the fittings etc it really adds up quickly if doing a external setup.
3 hours ago, mjrstar said:You could mount the baffle off the fuel pump cradle, from memory the fg falcon has a plastic tank and cradle thing the kind of clips in with a spring loaded nubbon.
Good idea! And could fill the rest with foam to help stop it moving as well.
-
1 hour ago, Tiger Tamer said:
Thanks for your replies Hyperblade. If I don't need to run a return line then that will be a bonus. Fitting an internal pump to the Hillman tank would require a fair few mods as the access hole is for the sender only and isn't very large. The guy in Canada used the fuel pump from the s2000 and shortened it and mounted the Minx sender to the side of the pump but enlarged the access hole with what he could remove from the Honda tank (without blowing himself up).
I think I will have to go with a external pump mounted near the bottom of the tank to feed a surge tank with an inner pump to feed the engine with an external regulator. I will look into the dampener. I have a pump that is reasonably quiet (nz made) which should make a good pump the feed the surge tank.
If I don't use a surge tank and can't baffle the outlet then it will really shorten the distance I can do between fills as I would have to fill up again at 1/4 tank.
Just for reference if you do decide to chop up the original tank (which is more then doable)
Here's the starlet tank that was running the altezza pump (ignore all the other shit, it's mostly redundant).
As long as you get the height of the pickup right e.g 2mm off bottom and run some baffling you would be fine.
He ran basically what was like Icecream sized square at the bottom around the pump with a couple of holes (and return from regulator feeding into it), this was pretty good even on the track until the welds broke and it started rattling around.
Granted he did blow it up in his face while welding it... but from what i've read if you purge a fuel tank correctly it's actually a straight forward job from that point of just standard welding.
Yours has a relatively flat surface too, I would just cut it all out put a plate on top, grab a fuel pump setup from a modern car like a toyota/honda and do another fuel sender hole.
-
1
-
1
-
-
-
15 hours ago, Tiger Tamer said:
I have been thinking about the fuel system lately. I am going to need to get the happy juice to the engine.
I see that Honda had a regulated non return system set at 60psi.
The fuel tank is mounted under the boot floor and its fuel exit is from the bottom of the tank as normal for car with a mechanical fuel pump. I am going to have to fit a surge tank of some sort. Some surge tanks have internal pumps though I am not sure why they have more than one. If a surge tank has two pumps, is one to bring fuel from the tank to the surge tank and the other to supply it to the engine ?.
My initial thought was to mount a plain surge tank in the boot with a pump supplying it as the surge tank will be higher than the fuel tank, and then another supplying the engine. If I have a regulator set at 60psi then I shouldn't need a return line. Not having to plumb a return line would be helpful. Returning it all the way back to the tank would be a bit of a pain and then you have to plumb it in. Then if I used a surge tank with two pumps in it, would it replace the two external pumps, which would save a lot of external mounting and fabrication, noise etc.
Cheers
Most fuel pumps don't like sucking (they need to have a head of petrol above them), so the 2nd pump in a surge tank is for those cars that need a higher volume of fuel sent to the rail (or redundancy for race cars).
I run a proper lift pump in the main tank so that it can run dry without killing it and it's not doing as much work as a high pressure fuel pump. In particular I run this one:
https://msel.co.nz/fuel-pump-low-pressure-in-tank/
I ran returnless setup when I had the 3sge engine + altezza fuel pump in my car (it was retro fitted into the existing starlet tank), all you need is an in tank regulator which looks like this: (heaps of OEM options) it's just a fixed regulator.
I would recommend a fuel dampener on the rail as well as we saw some interesting spikes with my k20 on the dyno when the injectors closed.
The advantage with return style is that if you are running a supercharger/turbo you can have the regulator in the engine bay referenced to manifold pressure, so you can increase the pressure as boost goes up.
If you plan to always stay NA then returnless will be perfectly fine.
-
1
-
-
Always cool to see top end technology slowly making it's way slowly down to the consumer market (starting at £4990 so give it another 5 years)
https://samuraimachinetools.com/
-
18 minutes ago, ajg193 said:
That's lush, I'd love to get a dividing head one day. Those drills will be worth their weight in gold over the years.
Skylarc has a few I saw, just a shame they normally go for mega dollars
-
- Popular Post
1 hour ago, Valiant said:Story Please.
It was a friends race car (5 of them took it up north to do the 24 hour race and are planning to do it again this year), it was on trailer under cover up his drive in Hillmorton.
They stole it on Thursday night damaging house and fence getting it out.
The last confirmed sighting of it was after 5:45pm going past Hellers on main north highway.
We have been posting in all the local facebook communities (+media) trying to get other sightings without much luck. So we knew it was likely still close to Christchurch.
8:42am this morning someone posted on facebook they had found a car and trailer pushed into the trees in Belfast Christchurch, friend was quickly tagged and picked it up.
Damaged window, front grill, bumper, but pretty much all there.
Best guess is it became to hot to handle and so was dumped. But interesting that it was dumped back into town, would suggest that things are going on slightly further out of town that some people don't want people to investigate further...
There were certainly a large number of very unhappy people looking for it and it was only a matter of time until we found it. But very glad to get it back in its current state.
Highly recommend everyone fit a GPS tracker, would have made this process a lot quicker and easier.
-
23
-
Car and trailer have been found.
-
6
-
2
-
-
-
15 hours ago, kpr said:
one word -> packaging
they will be aiming for the 3rd harmonic (itb's, the skunk2 maybe even 4th) im aiming for the 2nd, which is stronger = more power
tapered is said to accelerate the air. maybe. but are also losses in the pipe, so need to go bigger further from head to keep flow the same as. real world isn't much effective length difference with taper, unless is way too much. or turns into a massive bell mouth, which will act like the pipe ends part way down the bellmouth into the runner, rather than the face. in your case yeah i would taper out soon as get past the throttle plate.
Example of engine not caring too much if runners are too big; The runners on the manifold i made are 2.25" tube. think its 53 or 54mm id. half way around the bend it starts tapering down to the port. so yeah its big. bigger than the rbc intake and huge compared to the stock k24 manifold. but still gains power right down at 4000rpm. close to 10% at that point, so not a small gain either.
Another example. The only place my 4age with 52mm throttles drops below a stock engine is under 2000rpm.
Ahh that would make logical sense.
I'm not sure Skunk2 were aiming for any harmonic it looks more like it's designed for turbos.
320mm long looks close to a lot of things, may have to curve the velocity stacks to fit that in but that's all doable if being 3d printed. Will be another learning experience.
Thanks for the feedback!
-
5 hours ago, Roman said:
Hey I've got a standard S1000RR airbox - but I bought the wrong one.
It didnt quite fit because it must be the box for the slightly different variation of throttles from the earlier or later ones.
However it was definitely interesting to look at the mechanism for how it adjusts trumpet length, and the injector positions.
My consensus was that it was interesting to look at, but I dont think it would have added enough benefit for a car engine to be worth buying another one that fit correctly when adding to a car engine.
What I mean is, the box has shorter runners for higher rpm. But those bikes run to 14,000rpm so "low" rpm might be below 10k haha.
It's got a massive span of rpm it needs to operate compared to a car engine, which is why I think the dual length runner was valuable.
Also why the outer injectors earned their keep.
It was also interesting that the position of the outer injectors was so incredibly far from the runners, when the upper trumpets were lifted up for high rpm.
It must have essentially just been fogging the whole airbox. Like maybe... 150mm away from start of the bellmouth.
I will take some pictures and measurements when I'm next over where it is.
Can send it to your for cost of post if you're interested but it wont fit.
Those are good points about dealing with the rev range. I've looked at the videos of how it works and it is a very clever design in it's simplicity.
Still want to try it just to see the impact, I'm trying to get everything out of a stock K20 without opening it, so every little bit counts!
3 hours ago, kpr said:Yup, thats the same inlet test i was referring to.
Have you looked into s65 bmw throttles? they are 52mm, spacing should be pretty close for k series. the also have an oval outlet similar shape to the port. Have a separate dbw module that can be used if wanted to go that way. but is known to crap out.
I'd probably target 8000rpm maybe a touch under for your intake runner length. about 320mm from port face should get you ballpark. you want to get the intake tuning right where the engine naturally wants to make peak power. will make more power and fatten it up that way. rather than kinda trying to force it to make more power right up top. like your current intake looks to be doing. The VCT (cam timing) is also your friend here. you can use it to hang onto the power past peak a bit longer. If do everything right it should at least match the power it has now right up top 8500- 9k and make a bunch more 7500- 8000rpm plus more through the mid range
The runner length on the manifold in video is around the 350mm mark, as was targeting bit lower rpm.
Skunk 2 Ultra Street Manifold Runners
Just measured the Skunk 2 Ultra street Manifold runners as a data point.
These are all rough measurements as it's still on car and I'm not taking it off as it's a full days job (one of the reasons why I want to go to ITB's).
Runner length 155mm from port face to velocity stack tip (estimated)
Outer diameter where runner goes into manifold is 60.50mm, I think there is a fair bit of wall thickness assume 5mm which would make 50.50mm inside diameter.
S65 ITB's
S65 ITB's are out of my price range at the moment, plus the ones I have are a seriously nice bit of kit in terms of packaging and weight. I'm happy to use these ones to get experience with them, if they work better then what I have then that means I can sell the old skunk2 setup and look at other options. Will only cost me the ITB's and filament which is not a lot in comparison to off the shelf ITB's, plus i'm now sold on electronic ITB's since i've spent time and wired for them (obviously can still run cable if I need to), but not a chance I'm going with dbw module that's know to crap out...
I had looked at the efi hardware ones back when i was first looking for options, but they add up quickly with all the linkage and accessories needed.
Runner Length
So in terms of runner length for the Jenvey ITB's (EP3 version BUT NOT the Tegiwa compromised version) they look to me
Runner - ITB - Velocity Stacks = Total
85mm - 66mm(tapered) - 90mm(tapered) = 241mm
So I was planning to match that with
85mm - 78mm(tapered) - 78mm(tapered) = 241mm
But based on your suggestion it would be
85mm - 78mm(tapered) - 157mm = 320mm
So it's interesting to see such a big difference between your suggestion and theirs!
How does a tapered velocity stack affect things, my thinking is that as it's expanding it's slowing the pressure waves, so making it behave as if it's a longer velocity stack? How do you calculate that effect into it?
-
19 hours ago, Roman said:
Okay soooo
They had 184.5 wheel horsepower.
Then fitted ITB, and now they have 185.6 wheel horsepower.
So a 1.1 horsepower gain in real life.
But they now for some reason have 60.4 horsepower drivetrain loss instead of 56.6 horsepower drivetrain loss.
Did someone pour sand in the gearbox when doing ITB swap? haha.
This is why I hate "at engine" power figures.You have to love the drivetrain loss going up just at the end of the graph to produce a nice curve, very convenient for them...
To be fair the ambient temperature was different on the day.
But yeah, people need to stop with BS made up figures.
16 hours ago, kpr said:As above, I have been looking at some of the stuff they post. as been playing with a k24. They quote all these different gains in bhp, but the wheel hp on the same graph says something different. also mega driveline losses. Ive roughly overlaid the graphs blue is the wheel hp. red "engine" power. light lines stock intake, dark itb.
Looking at the wheel power. the stock intake manifold would be a quicker car. unless you could run between 8000 & 9000 rpm the whole time. even then wouldnt be anything in it.
Why, The itb's will probably flow more. but the runners are way to short to make any jam over the whole rev range. stock inlet will be running out of flow and or slightly too long to make power at 9k
ITB's only work good if you dial in the runner length and have the flow to go with it.
Seems to be super common with K series stuff. even the factory inlets. They are too short with big runners. or long with small runners.
I think those itb's you have will be a touch on the small side. possibly ok. but can get away with over sizing the intake a bit. not so much under sizing it. if make the runners small enough to gain in the bottom end (talking rpm you will never use in circuit car) will lose top end. if a bit too big, not much happens. not trying to lecture you, just wouldn't be fun to have to do it twice if you didn't have to.This is the intake i just made for k24. Big long runners. gains everywhere over RBC honda inlet. which is spose to make more peak power that the stock ep3 one they compared the itbs too.
Yep, here's another brilliant one from them, I'm sure you've already looked at it.
https://www.tegiwaimports.com/blog/?p=2443
I got caught out by this one when I brought my current ultra street manifold, i'm much more careful looking at these things now.
Lecture away! (happy for anyone too), I always like considering all the possibilities and discussing this stuff with people who have actual real world experience.
I agree slightly larger ITB's would be ideal so that you have a bit of wiggle room, but the feedback I've had is the normal Jenvey ITB's worked the best on a dyno(on built k20 in CRX) when comparing multiple different types, so if i match them in design I'm confident that it should perform at least better than the skunk2 intake I have currently.
But I'm limited by what you can easily get off motorbikes due to the pricing, I had a look around at other options, but nothing stood out.
However I do have a couple of other things planned to throw into the mix.
- Outboard injection.
- Variable velocity stacks (I'm on the hunt for a standard S1000RR airbox to get the mechanism)
- Intake will be using ram air to create pressure through filter and into air box.
- I have heaps of room to play around with lengths of stacks (which will be 3d printed so not expensive to make).
Do you have any good calculators you use for working out lengths of intake runners? I also need to find the measurement of valve to intake flange to use in them.
Just for reference car normally runs between 6000 to 9000rpm in a lap with lowest being 4700 rpm at hairpin. Being light and having the torque allows me to use more of the rev range, which helps with not overworking the tyres.
-
The last club day of the season (I was out in first round so not worried about points) was coming up and it was looking wet
So I thought it would be a good opportunity to get the the car out for another shakedown of the new wiring, and get some experience in the wet (I've never driven in the wet).
So first time out on a wet track in qualifying, i put it on pole...
Race 1
Turns out it goes really good in the wet. Allowing me to take my first win by 30s over 2nd place (he sand bagged a bit after he accidently hit pit limiter and saw me race off into the distance).
I managed a 1:42.5 which is I'm absolutely stoked with, that's only 7s off my dry time, and there was a little more in it (and that's with no changes from current dry setup).
Also it confirmed that things like the wipers, lights and demisting (not running any, instead I'm using the heat from exhaust + radiator) all worked as expected.
The wet's i ran are 4 year old ex Michelin TRS, and are absolutely amazing, it really was like driving in the dry, they are super soft and it shows as another competitor who is normally slightly faster in dry then me had older harder different brand wets and was 12s off my time.
But also the weight of the car and it's handling characteristics show it's driveable/chuckable nature.
Race 2
Race 2 was a handicap race and I was 60s behind first pack, unfortunately the guy who came 2nd place in 1st race was 15s in front of me, and he picked his pace up to match mine, i did manage to get within 9s of him on a damp track (rain had stopped).
I came out of the day actually feeling excited to potentially race in the wet in the future, where as before I was very nervous, so that's also a massive win.
ITBS
Interestingly enough Tegiwa have just come out with some Jenvey ITB's to fit an EP3, they are very heavily compromised to fit in the engine bay, but do have some dyno charts.
Check out the dyno results and see what you think about the results and claims...
https://www.tegiwaimports.com/blog/?p=6297
QuoteA run of 251.1bhp with 161.1 lbf.ft meant the kit had improved performance with an additional 13.8bhp! Of course, dyno figures aren’t the be all and end all of everything, it’s largely about the experience on the road. As we all know, there’s not much that comes close to the noise of a set of ITB’s screaming all the way to 9,000rpm which is a huge factor when it comes to deciding what option to go down when tuning your K20.
Before:
After:
Let me know your thoughts in my discussion thread here:
-
7
-
-
On 01/05/2023 at 16:47, Tiger Tamer said:
I need to reinstall the main water pump housing and they don't use a gasket. I see there is a sealer made by Honda called Honda bond HT. Do I need to use this or will any good RT sealer work just as well ?. What ever has been used seems fairly well bonded to the aluminum so I will have to be careful not to damage the mating surface.
Is copper coat good to use on the bolt threads with aluminum or is there something better I should use ?
Cheers
Loctite the bolts.
I have a water blanking plate on my k20, and lost 1 bolt, and had 2 back out (out of 4), there is a lot of vibration with these engines (granted the blanking plate is also not designed great either), I was lucky as the blanking plate runs orings but it could have been a lot worse.
-
1
-
-
26 minutes ago, Roman said:
Nice work on that DTM panel! Looks good, been thinking about doing something similar.
However will you be doing anything to index them or add a keyway or something, so you cant plug the wrong plug into the wrong one?
Or colour coding them or something.
(I'm here to steal ideas)Yeah so all those thoughts crossed my mind when I did it. At the moment I have none of that.
Each connector is numbered on the loom and the bulkhead plate is numbered, but that's obviously not a fool proof solution.
Keying would be hard, you would have to machine the connectors down to put it in, and I'm not sure how much material is there to do that.
I had thought of printing color coded wrappers for them then glueing them on.
Can't use dummy pins as each connector doesn't have many to begin with.
I have made each connector very similar, e.g. 12v always on pin 1, 5v on 2, sensor ground 3, so it limits the risk a little bit, and coils/injectors are all interchangeable with no risk.
However my biggest concern is swapping the EWP with the ECU ground, if that happens then it's a straight path from fuse to ground.
So no solid solution at present, but open to ideas.
-
1
-
-
- Popular Post
ITB's Next Step
So the wiring is now done just needing testing.
The ITB's are a long term thing I need to slowly work through.
So while rewiring I pulled the manifold off so I could measure the ports and create a flange in CAD so I could slowly work on the manifold adapter.
So much crap on the internet
I did a lot of research on the internet around K20 ITB's and the port sizing, and can confidently say some manufacturers have both the port angle and port size wrong in their drawings (and that's their job to get right) Jenvey are definitely the ones who have it the dimensions right and that's backed up by feedback from someone who has tested a few and found them the best.
The jenvey ones are 48mm and everyone says that bigger then that is better (e.g. 52-54mm), but that ultimately depends entirely on where the throttle blade is positioned with the system.
e.g on the following diagram, A, B and C are all different plate sizes but really have no impact on the amount of air being ingested, however position does have an impact on response and driveability (closer to head being better).
So the Honda K20a CL7 port size is equivalent to 46mm throttle plate, which means if you put the throttle plate at B (48mm) you have accounted for the restriction it causes.
Jenvey looks to keep a straight section (no increase/decrease in size) of 46mm diameter for a length of 85mm from port to throttle body flange. I suspect that is because you don't want to take energy away from the air by trying to increase it's velocity just before it goes into the head, but could also be packaging etc. I'm just speculating here.
Additionally Jenvey have the port angle at 17.5 degrees, which when I measure is perfect for dead center (vertically) of the port as it narrows. Where as they others have 14/15 degrees which means the top side has a sharper angle then the bottom (which is flat).
So I can see why Jenvey perform, their experience shows in actually getting the basics right.
So they are the ones to copy as I can't afford their full kit
BMW S1000RR ITB's
Now the S1000RR ITB's are 53mm entry, 48mm plate and 42.84mm exit with a 3.5 degree taper on walls.
The exit is not good if port size is 46mm., however I'm confident I can bore them out with a little effort on the lathe to 46mm which would be perfect, I only need to bore 10mm into them, so don't have to worry about the throttle plate.
So I pulled them apart to see how hard it was and if it was possible to put each half on the lathe as is without having to completely dismantle the plates
Then they wouldn't go back together, a small bit of panicking later I was thinking I would have to dismantle them which would then mean they needed to be resynced.
But in the end I 3d printed a tool that now allows me to put them back together as they were from factory, so that's a massive win.
Bore spacing was the other worry the ITB's are roughly 83-82-83mm and the CL7 is 94mm, but it turns out that it's close enough that it will be fine.
So I can proceed with the ITB's and the design of the manifold to suit them.
My intention is to mount the standard Honda injectors into the manifold in the same place as the Skunk2 manifold (close to head) so that the transition of the tune to the ITB's is easier, then setup outboard injectors at a later stage (and just block up the BMW ports).
I'm not rushing this so it will be done when it's done.
Just in comparison here is what others have done to fit bike ITB's to a Honda K series.
https://www.jimbositb.com/product-page/throttle-body-adapter-plate-k24
Feel free to tell me I'm an idiot here;
-
14
-
1
CHCH - Need Oscilloscope and someone who can operate it to help diagnosis issue
in South Island Region
Posted
Just Crank and Intake/Exhaust Cams.
From what I have read on their forums what they advertise takes that into account, so you can actually go higher then stated normally as your not maxing them all out.
Often people put a divider on the honda speed sensor, but the latest Link ECU's should be capable of handling it (and they do a plugin version now)