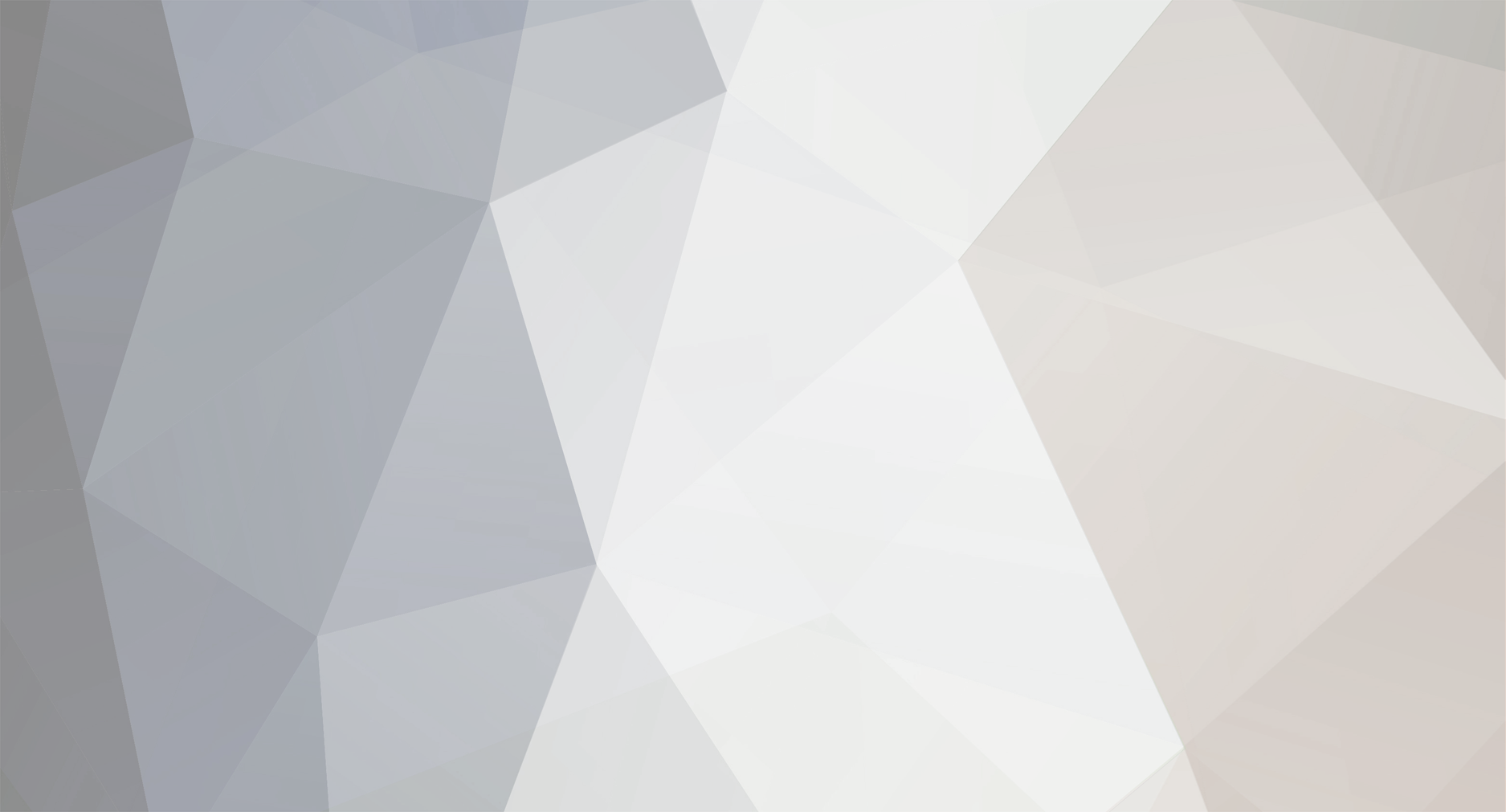
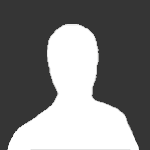
Ja1lb8
Members-
Posts
289 -
Joined
-
Last visited
-
Days Won
2
Content Type
Forums
Downloads
Events
Gallery
Everything posted by Ja1lb8
-
Finally got the car back from the upolsterers. Looks decent, got the boot done as well. Had a crack at covering the dash in vinyl which came out ok. Want to get a proper moulded remanufactured dashpad but the dashboard place needs the steel frame to make a mould off which is a bit hard because its welded in so have to cut the bulkhead out of a car and take it to them for that to happen. Otherwise continue on with putting it back together
-
Blasted and painted anything I could. Pretty tedious work bit real happy with the result. Think from memory I replaced the bottoms of those inner guard things because they were all rust fucked too
- 28 replies
-
- 11
-
-
Sandblasted the fuel tank and was rusted from the outside in. Ended up brazing up the holes and putting gas tank sealer stuff in it.Was nice and clean inside bit wanted to seal up where id been welding. Seems to have worked a treat.
-
all out of order bit found more photos of rust repairs to boot floor , inner and outer rear guards, just everywhere really
-
Anyone had any experience with refurbishing steel chrome wheels. Talked to old barry at chromers and they used to do plenty of them . Have to machine the centre out, chrome the barrel then reweld. Not willing to touch now cause of the libility welding wheels. Elite wheels in chch are happy enough to weld them but cant do the chroming. Any suggestions welcome
-
Had all these thoughts. Cause jap import going to get it complied with original running gear and drive it. Then build up a spare chassis with engine and brakes etc
-
- 28 replies
-
- 23
-
-
- 28 replies
-
- 11
-
-
rear seat recovered, front seat used the origanil upolstery but rebuilt the foam and srpings in it, sound deadening fitted
-
2 litres of neck snapping fury, got it bodgied up and running so could drive it and get interior finished, goes surprisingly well ....for now
-
-
Massive thanks to my dad for panelbeating and polishing every single piece of stainless on the car of which theres a lot. Hate to think how long that took Also a big thanks to @toy-mota fior selling me his nos grille and surround thing, It really finishes off the front of the car
- 28 replies
-
- 12
-
-
Front indicator lenses were rubbish, got talking to gc in aussie who was kind enough to sell me a mint spare set he had
-
somewhere along the way I got all the crhome redone , dunno where all the photos are bit heres one of the mirrors finished Had too diegrind out all the corroded parts and fill and sand without scratching my new chome, came up all good though. Same process with the door handles and other parts made up out of that cast muck metal rubbish
-
In the meantime Id been giving the engine a tidy up and all the other parts a birthday so I could start putting it together when It came home Hardest part of this whole builds been tracking down rubbers off other models and cars to adapt because cant buy anything for this off the shelf
-
- 28 replies
-
- 14
-
-
And because Im impatant I had to make the vinyl roof trim on the car after it was painted which is definately a dumb thing to do. Managed without any scratches which really surprised me Used brass this time , heeps easier to work with and came out real well
-
- 28 replies
-
- 16
-
-
Tryed making the stainless trim thats missing where the vinyl roof finishs, Used some old stainless off a hillman and fit it on a wreck that my brother has. Think it could have worked bit the stainless was hard to work with and didnt turn out as nice as I wanted
-
- 28 replies
-
- 15
-
-
Heeps of work going on in the background while the body was getting done, sourced alot of parts from japan, sandblast and painted chassis, was all in pretty good nick, think it had only done 96000kms
-
Car went off the panel beaters and I was blown away at how quick things happened. Usually would take me a year or more to sort all this mess out bit not three weeks later I get a call asking what colour I want it
- 28 replies
-
- 12
-
-
Cause couldnt help myself and what toyota doesnt need a v12 The whole front sump crossmember steering box in the way makes this pretty unlikely to work but dreams are free
-
Surprised myself and had a few weeks left so started into the rust repairs Came up pretty well, no filler needed
- 28 replies
-
- 10
-
-
So did something I never do and went and booked in a panel beater. Was due in a months time so I had a deadline which is the only way im likely to get things done. Stripped car down, plenty of rust