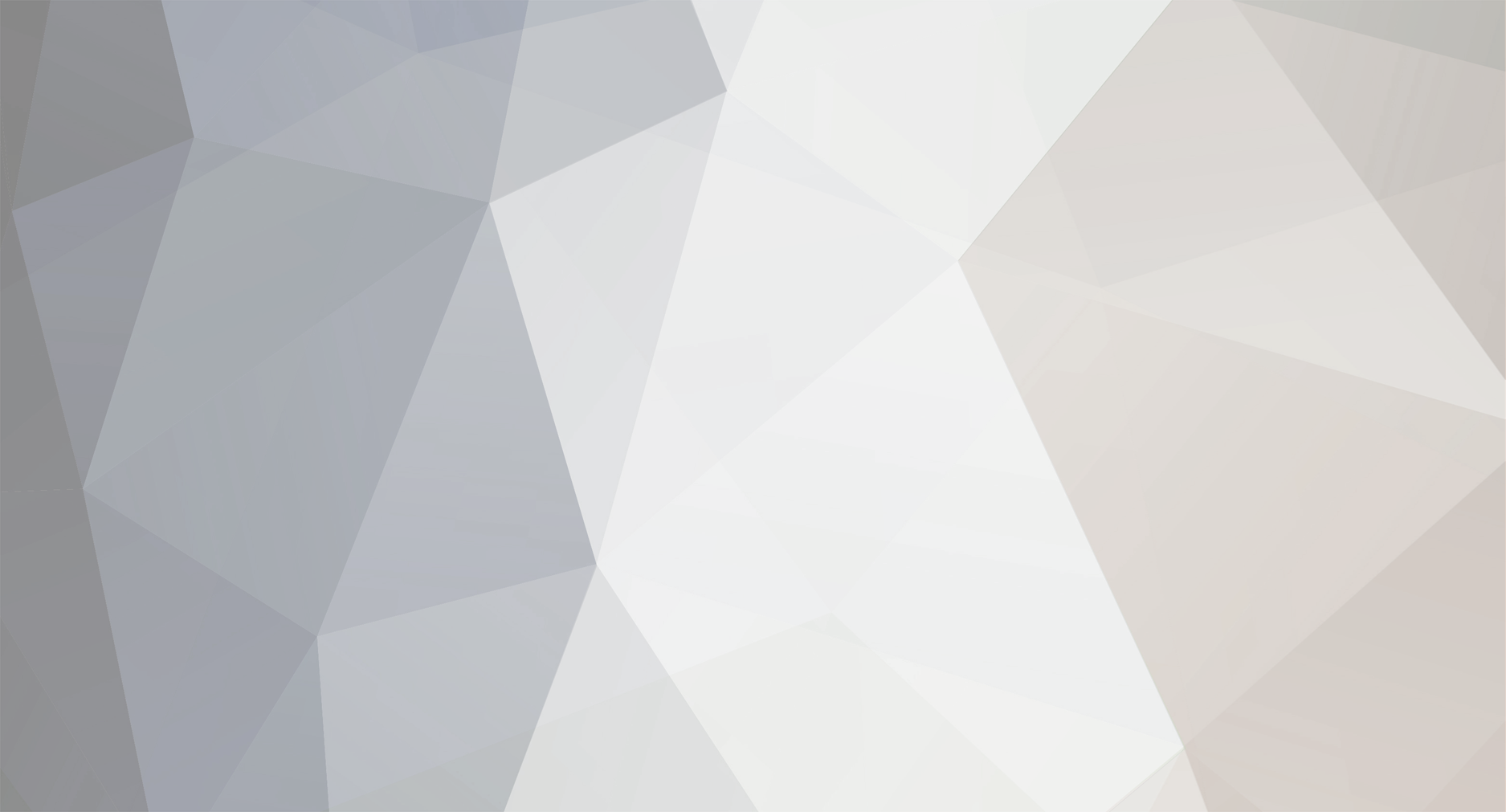
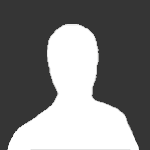
dwlee
-
Posts
156 -
Joined
-
Last visited
Posts posted by dwlee
-
-
Sorry Tom, I couldn't find the shroud. It was from an early L200.
-
1
-
-
I might have a shroud that may fit. I'll have a look in my stash and let you know.
-
The standard leaf springs as pretty soft and if you have them reset you may need to add another leaf. I had to do this with the 76 and I'm likely to do it again with the 75. I'm using early land cruiser (Fj40) shocks in the rear.
-
1
-
-
Looking good with the stripe. What do you want to do with the suspension? Just lower it a bit, replace bushings and shocks or are you wanting to go it further?
-
Good luck with the wof. It's certainly looking great! I bet you can't wait to go for a drive on a hot day with all the windows down listening to the music from the carbs.
-
1
-
-
The paint job looks great. I bet you can't wait to get it back on the road.
-
Keep up the good work. The new carbs will sound fantastic.
-
1
-
-
When I was looking for boot rubber for the GTO Basis were very helpful, but at that time (2012) they didn't have anything that fitted correctly. I ended up using the one from Scotts old auto rubber and did does the job pretty well, but it was tight until the rubber settled down.
-
1
-
-
Quote23 hours ago, Roman said:
God damn I really just didnt need to watch that infusion / vaccum bagging tutorial on making that bonnet.
Holy shit that was awesome!
Have you watched the pattern making / prepreg vids yet as they are just as good.
-
1
-
-
These guys have some good videos https://www.youtube.com/user/easycompositestv/
-
1
-
-
Have you confirmed that the studs you have are correct for 4g63 mains as they should be m10 with 1.25 pitch. You may have 7bolt head studs, which are m11 x 1.25 pitch.
Again what is the part number of the studs you do have?
-
What is the part number of the ones you have?
As far as I know the mains are near enough the same for sohc and dohc 6 or 7 bolt.
RPW sell the same kit for them all http://shop.rpw.com.au/online-store/products-by-vehicle-manufacturer-2/mitsubishi/mitsubishi-starion-turbo/engine-products-starion-turbo-4g63/main-stud-kit-mitsubishi-4g63-detail.html but you are better dealing with Sta parts as it will be much cheaper http://www.staparts.co.nz/View-A-Product?id=401&Productid=Main stud kit Mitsubishi 2.0L 4G63 dohc 16 valve 2-bolt hex
-
What you need to find is Mitsubishi's electronic catalog either CAPS (older) or ASA (newer) so you can look up bolts etc. Also, check out Austarion forum as they will have access to the Starion parts catalog.
-
The 4g61 is a dohc 16 valve 1.6 motor that has hydraulic lash adjusters. I assume by 6g64 you meant 4g64?
-
Definitely not guaranteed, but you're a lot closer to something that might work if its from the same series. The 4g6x series was in production for over 25 years and there were quite a few change over that time. Some are interchangable without and changes, some require minor changes and others require alot of work and not worth the effort.
What was the donor car/year for the 4g63 engine you are rebuilding?
-
No, the 4g5x (Astron) series have a completely different bore spacing to the 4g6x (Sirius) series. The bore spacing within a series is the same, but head bolt diameter can vary with earlier being 12mm reusable and later being 11mm that requires replacement. Also, the inlet/outlet swap sides around 1996 in the 4g6x. Have a look around http://www.projectzerog.com/ as there it has a lot of info regarding a swap from SOHC to DOHC.
I'm not aware of any 8 valve SOHC 4g6x with larger valve but there is the option of 12 valve dash head with two lets valves.
-
Best bet as others have said is get it colour match. My 75 has Himalayan Blue, but my 76 originally had Tahitian Blue. I suspect your car was/is Himalayan Blue AC10178. NZ cars came with the standard JDM colours plus a few extras like gold and yellow. A good guide to the colour options strips can be found at http://www.galantgto.net/option-stripe.html
By the way the wheels and whitewalls look great.
-
1
-
-
When I put semi-sealed units in mine the locator tabs matched one of the cups and not the other cup. The units I used had thin metal tabs in a sort of a loop and I was able to manipulate the tab so that they fitted into the cup correctly. The difference in the cups is to stop people putting the wrong headlight in the wrong location so the high/low has different taps to single high. I put in two sets of high/low semi-sealed units and just running one set as high.
Shame about the rust/bog/dent.
-
Any increase in headlight wattage over factory and you should be running them off relays in the engine bay. Even with original wattage headlights you would be amazed how much brighter they shine when run from relays.
-
I assume you want to be able to set the nominal zero position from which you advance and retard the cam and set that as your base position? The 12 degrees measurement maybe fully retarded and that's the reason they set the minimum duty cycle at 20%?
Some basics of PID control are that the input to the controller is the difference between desired value and the actual value, the error. The control signal is made up of the sum of three components that are related to the error:
- Proportional: proportional gain multiplied by the error. Think of it as the error is this much so we will apply that much control signal. Zero error equals no proportional component to the control signal
- Integral: the integral gain times the area under the error curve. Think of as the part that drives the control signal so that eventually actual error goes to zero.
- Differential: the derivative gain time the slope of the error curve. Think of it as the part that tries to resist the rate of error change.
The problem with PID controllers is that the measurement of the actual value is noisy and the real physical actuators have limits to how much signal they can transmit and the rate at which they can change their output. The noisy measurements will cause that noise to be amplified by the differential component of the controller. The physical limits of the actuator will cause problems such as; integrator windup (too higher integral gain) and or oscillation (too higher derivative gain). To higher proportional gain can cause actuator saturation.
In your case increasing the level of filtering will reduce the impact of measurement noise as will reducing the derivative gain. I would not recommend changing the integral gain and to a lesser extent the proportional gain. The best way to manually tune PID gains is to perform step change tests where you change the desired position from one value to another and look a how the actual position changes in the logs.
-
Roman, have you tried a custom PID setup? Looking at the default setting in Link's Altezza base map the filtering is set to the lowest level and derivative gain looks quite high (but hard to know without knowledge of how the algorithm was coded). The high derivative gain and a noisy position signal may cause oscillation in the control signal. Also, the large difference between the actual position and the target like at the start of the log might cause integrator windup, which can cause strange things to happen, so best to fix the offset error (hopefully link have a good anti-windup strategy build into their controller).
-
2
-
-
Thanks for the photos. The ends look a lot better than I thought. Any extra window rattles on the long trip? Over tightening will do that to the bearing as will not packing the bearing with sufficient grease. With the wheels are looking good.
-
Picture of the ends would be great.
-
The oem rubbers can be temperamental with the amount of tension applied and if it wrong they split as you've found. I've always been curious how those Rare Spares generic rubbers fit. They actual look quite good from your photos and a lot better than I thought they would. What is the fit at the ends like?
4G92 RS Mivec ecu confusion
in General Car Chat
Posted
You could look at some of the info that's on http://www.mivec.co.nz/forums/index.php