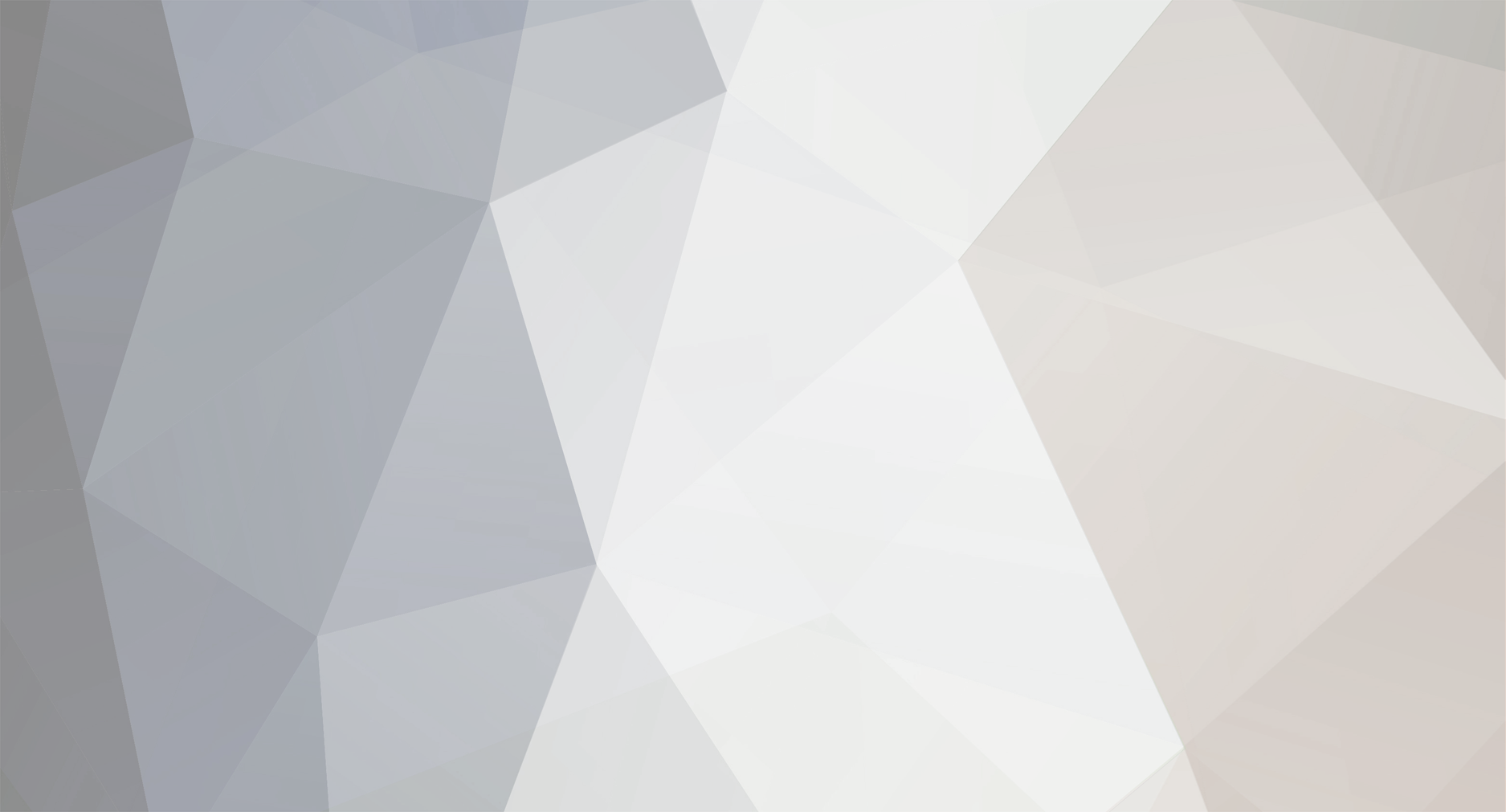
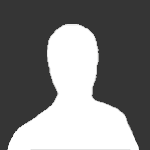
Shortcut
New Members-
Posts
17 -
Joined
-
Last visited
About Shortcut
- Birthday 04/02/1963
Profile Information
-
Gender
Male
-
Interests
Got me small home workshop and fix/recondition motor vehicle cylinder heads for a paying hobby - retired police - self taught automotive machining and cylinder head repair (kindly taken by elderly german friend 76 years old he's deceased now) - he taught me all his tricks and trade he had learnt over a career spanning 52 years in auto repair, he needed younger hands to continue earning a buck, I needed a second income and loved anything mechanical , oily and broken.
Together we had a great time in his home workshop.
Converted
-
Local Area
Outside NZ
Shortcut's Achievements

Member (2/5)
34
Reputation
-
Shortcuts 1971 Mazda B1500 Proceed UTE rebuild
Shortcut replied to Shortcut's topic in Projects and Build Ups
apology for long time not posting - busy with life - hope you all well and healthy - progress - I managed to source new pistons - +rings+piston sleeves+camshaft bearings+ full gasket set and other things - all new from USA - under the banner of Hyster UA (Mazda engine) - same thing - after getting the diff re-done +new diff bearings and backlash corrected - I cannot seem to fit back the old half shafts (using the previous shims) - I did mark them passenger and driver side - they are back into their respective positions - ok - I know tolerances have changed with the new bearings - can anyone perhaps tell my why the bloke before me had put a 5mm "spacer" before the inner wheel bearing race - and shouldered it up onto the half shaft shoulder - the added the bearing??/ also I will post pics of my new white walls - soon as I can re-take pics again with my phone also my half shafts are now touching the diff inside - as engineers blue transfers across - any ideas anyone for the critics - if I have not offended you yet......... please be patient I will get to you as soon as possible - thank you -
Shortcuts 1971 Mazda B1500 Proceed UTE rebuild
Shortcut replied to Shortcut's topic in Projects and Build Ups
I was having headaches removing the side shaft bearings (rear shafts that go into the rear differential) - maybe because they were pressed bearings, and or old age - anyway made me a "chinese hammer" to knock the bearings out in reverse - 1. take a hollow iron "tube" approx 2.5mm wall thickness with an ID(inside diameter )that fits neatly over the side shaft axle right down to the shrouded bearing inner race - exposed face 2. make a "slide hammer" aka chinese hammer here 3. put a "hammer stop" at the top end of the overlaying shaft FIRST - FIT THE hammer SLIDE onto the hollow overlaying SHAFT - ie. assemble it first for operation - then fit the hollow overlaying shaft down onto the side shaft axle and let drop it all down till it touches the bearing inner race (find a way to hold your "hammer slide" part up near the "top stop" part - so you can weld in peace - i used a piece of wire) then weld the bottom part of the hollow overlaying shaft that's in contact to the bearing inner race I used stainless wire +tig -stainless sticks better then baby shite to some metals while the weld is still hot and expanding the bearing race - slide (knock) the hammer in reverse (thats why its called a chinese one) - literally 30 seconds plus - poof - out they come - 4-5-6 hard knocks GRIND off the first bearing inner race (from the overlaying shaft end tip) - and reload -ie. reweld the overlaying tube end onto the second bearing you will see how I battled at first to get the first bearing out - I tried to grind it with mini grinder, no joy,.... knocked it, no joy...., tried to lever it, no joy.....and did not want to press it out - besides it would not fit into my press - AND the bearing shroud would have to take the pressure from the press - most difficult as you cannot get a cutter/blade into the surrounding bearing shroud to split the bearing inner race to release it's grip on the side shaft then "enter the dragon" - "chinese hammer" -presto !!!! - you also cannot hit/knock/press out the wheel bearing (with another method or device) as you may crack the cast iron bearing holding shroud if the bearing is a real tight fit - also the shroud design doesn't let you get in anywhere to remove the bearing as the back end of the side shaft is blocked off - this "chinese method" removes all the stress +knock+pull +pressing is going directly into the bearing race that must be removed - and the harder it's knock pulled the quicker it comes off. hope this makes sense from the pics - [/url] -
Shortcuts 1971 Mazda B1500 Proceed UTE rebuild
Shortcut replied to Shortcut's topic in Projects and Build Ups
getting new bearings for the differential then will adjust the backlash - thanks to YOU-TUBE lessons -
Shortcuts 1971 Mazda B1500 Proceed UTE rebuild
Shortcut replied to Shortcut's topic in Projects and Build Ups
everything was cleaned and rinsed properly after receiving a sand blasting from my wee little workshop in the backyard - then prepped with BLACK ETCH PRIMER, then oversprayed the next day with RAVEN BLACK DUCO (enamel) - should hold out well enough. - had plenty of hard rain for 2 days and I left the chassis standing out in the cold dew, wet rain, and sunshine - not even a rust powder mark appearing after 2 weeks - super - I think its gonna work well. same spray method and coating s for the chassis and all the parts - least about 2-3 coats everywhere the chassis only had surface rust on it when I started - figured no reason to sand blast it or powder coat it - used wire brush under power and it came out super - if it lasted 45 years before me and had no rust holes - it will outlive my wee little self anyway at least for another 45 years and I sure as hell won't be around so long still - so no worries here.!!! me battling a little to remove the rear side shaft bearings - seems the side shaft bearings are stuck onto the side shafts with baby shite. - press fitted no doubt - need to get them off without cracking the cast iron bearing shrouds. other wise we are all little tired but feeling grand. - later - if more pics needed please ask - -
Shortcuts 1971 Mazda B1500 Proceed UTE rebuild
Shortcut replied to Shortcut's topic in Projects and Build Ups
hoping these all come out good enough - my comp skills are real bad - "old -timers" stripped the Mazda down - blame it on "Maxted" -
Shortcuts 1971 Mazda B1500 Proceed UTE rebuild
Shortcut replied to Shortcut's topic in Projects and Build Ups
oki - I managed to source almost all of the parts I needed - including the 2 used engines (B1500 ones) with Standard crankshafts in them with standard "big-ends" (rod ends) - wonderful - as the crankshaft and main+big end bearings availibility was holding me back from keeping the "bakkie" (pick-up or utility) with it's original engine anybody youtube the "Mazda B1600 with skyline engine RB20 - straight six 2 liter engine I think ???? - sounds awesome - https://youtu.be/-_vkLql1SRo hope I did this computer reference thing correct? I cannabilised the best sleeves +pistons+rings to make up one good engine - specs look ok. stripped it down to the chassis (that's Maxteds fault - I am copying him) - all parts dismantled, at moment rebuilding EVERYTHING - not a single bolt remaining on the chassis - busy with learning how to take the backlash out of the differential - you tube will do that for me, I will post pics just need to get them reduced in size - getting there, lots to do back soon - nearly midnight here - -
Shortcuts 1971 Mazda B1500 Proceed UTE rebuild
Shortcut replied to Shortcut's topic in Projects and Build Ups
Hi Folks, the B1500 Mazda Proceed project is a GO it seems, I got me 2 used engines I found - and both cranks inside are still "STD" with "std" bearings on big ends(rod bearings) and mains so far the load bay has been removed and I am getting excited to tackle the job - never done this type thing before - don't know how much in gin n tonic it gonna cost me as well - I get thirsty when I work what is outstanding in the parts arena are the following: 1. big end bearings (rod bearings) - for love of me - i cannot seem to source them here (South Africa) - maybe another vehicles bearings will fit - 2. I would really like a spare distributor cap 3. original sleeves and pistons ( I can bore the B1500 sleeves to take B1600 pistons - compression height the same(42mm)+bore is only 3mm bigger - 75mm vs 78mm - the sleeves have walls of 6mm thick(possible - hmmm yes I would say) but B1600 is domed top piston and I will lose some compression - but I score on the bigger bore - should balance out somewhere in the middle - will have to have a head gasket made up to accomodate the bigger bore seems the old gaskets B1500 head gaskets were made to just cover the piston sleeves edges(firing wall) to stop people boring them bigger and thus also sell more piston sleeves instead maybe someone out there can sell me some rod bearings + me on PAYPAL and registered Ebay - meanwhile I got me a few sets of mains - all sizes - Std to 40thou - just in case will post update and pics as I go along now to buy some time somewhere? -
got me one these recently but am pulling me hair out - need new crankshaft and piston sleeve+pistons +rings+bearing rebuild kit -else a no go venture - any help with references on websites would be much appreciated takes Mazda AU 1484cc engine - found in Yale forklifts+HYSTER forklifts and some TCM forklifts