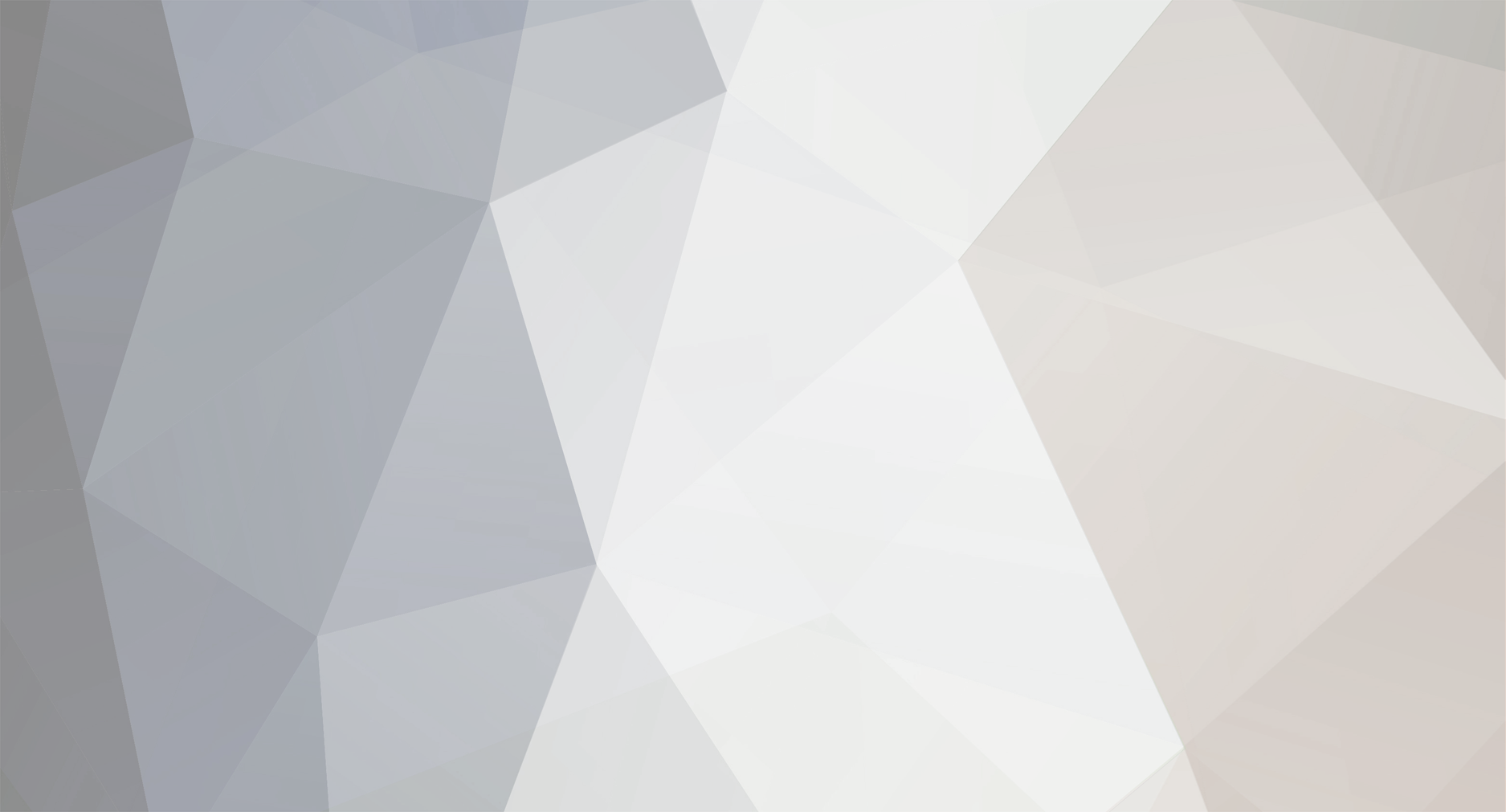
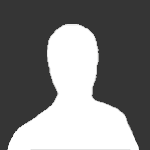
RS2J
-
Posts
170 -
Joined
-
Last visited
Posts posted by RS2J
-
-
Will have it available via dropbox in the near future is anyone doesn't want to torrent it. Just flick me a PM and i'll share the folder with ya
-
1
-
-
On the home straight of sanding now. One side done up to 600 grit, the other up to 120.
Next up will be heat treatment. Still yet to build the legs for the mini forge, but the burner is now complete - also visible in the above pic. The non burny end of the burner has the following assembly - pretty much just a valve and a couple of brass bits fitted/brazed together to attach a standard BBQ hose and fit it to the 15mm steel pipe. Have a couple of oriface options with a 0.8mm and 1.0mm option. Can just buy more caps and have different sized holes drilled if necessary
At the end of the day its just an oversized Bunsen Burner - hopefully enough to heat the forge up to the 800 degrees I need toe knife to reach before dunking it in oil
-
7
-
-
A lil Lancia action sitting on the work grounds.
-
3
-
-
So then is it heat treatment time? So was that just
File the bevel on then remove the file marks with the paper? What oil you useing for heat treatment?
Yeah, I should have followed up the bastard cut and second cut filing with a smooth cut file. Some of these file marks are a bit of a pain to remove even with 120 grit. once I've finished it to a reasonable standard, i'll heat treat after I've built the burner for my mini forge. Plan is either Canola or Peanut oil - whichever is cheapest that I can buya couple of litres in bulk. Then back to sanding up to 800 grit for a nice satin finish. Then its handle time, followed by sharpening and murders - I mean slicing onions. I may acid etch the blade with ferric chloride or hot vinegar before I put the handle on though. At least help a bit with corrosion resistance being carbon steel.
-
Shit that looks good!!!
Cheers! Started working on the other side but ran out of 120 grit tonight. 10 sheets burned through pretty quick! Thankfully the hard work is done by then and the 240 then 400 don't take nearly as much
-
- Popular Post
- Popular Post
Starting to look knifeish
-
12
-
And while we're at it. Here is the Mini "Trash Can" forge being cast. The lining is just Sand and Plaster of Paris with an 80mm PVC pipe in the centre to create the chamber. The old copper pipe to provide an entry for the blowtorch is placed on a slight angle to have the flame pointing slightly towards the rear to reduce the amount of flame coming out the front.
-
Yeah. Gauge plate is 01 tool steel.
I can tell you that after a bit of heat it ends up EXTREMELY hard. (Don't get components laser cut out of gauge plate and then expect to file up the edges)
Nice. O1 is easy to treat. Heat up til its non magnetic, dunk it in warm oil
-
1
-
-
We use quite a bit of gauge plate at work so was thinking that could be a go. But was thinking some tooling stainless could be better?
Stainless can be a bit of a bitch to have heat treated. If you can find someone who can heat treat 440C thats what they recommend to start with. Remember that the steel you use must be able to hardened in order for it to take a decent edge. O1 tool steel, 1070 or 1084 are usually the ones they recommend for beginners - simple carbon steels. The 1095 i'm using is a bit less forgiving they reckon.
Highly recommend looking up Walter Sorrells and Gough Customs on youtube and watching some vids.
-
I've been thinking bout having a go at this to. Did ya just start with a blank say 3mm wide?
Yeah bought a couple of 2" x 18" x 1/8" (about 3mm thick) flats of 1095 steel from the US (Damned if I could find it here!). Carved out the knife with a hacksaw and a file
Made a beveling jig similar to the ones you can find on YouTube
Current situation:
-
4
-
-
- Popular Post
- Popular Post
-
-
Considering selling. Feel free to register interest via PM
-
-
-
Holy crap thats awesome.
-
1
-
-
I also had the same issue back in the day with my old '75 MkII. As above, we had to modify a manual crossmember to reach across the tunnel. Passed WOF's for a few years until it got picked up and they demanded a cert. The car was only worth about $500 WOF'd and Reg's back in the day so sold it to a guy on a farm and it lived out its days as a paddock hack for his kids to learn on.
-
Jealous!
-
Holy crap that looks awesome
-
Grabbed some of the headlight buckets from Palmside after getting fluffed around on trademe by a couple of guys. Trial fit of the round headlights followed:
-
4
-
-
Been meaning to do this for a while. Thought i'd get onto it while the Mrs is crook and I have some nag free time. Good old Mighty Car mods vids for the win.
-
4
-
-
- Popular Post
- Popular Post
Spotted around campus here at work
-
15
-
-
Rare opportunity to drive this thing today. Made sure to get video for proof heh
-
2
-
Seedy Al's Lost Photo Films Archive
in General Car Chat
Posted
Nice! I'll have to dig up a bunch of pics I have from the '99 Nats and scan 'em